What drove USG to begin using Poka’s connected worker app on the factory floor?
Like a lot of companies, we have a very senior, tenured workforce and we were seeing a lot of retirements. At the same time, we were making a lot of investments in new equipment and processes to bring into the plant. That forced us to look at our training and how we communicated. We had a lack of multimedia incorporated into our work instructions. It was largely a paper-based system and we really wanted to improve our training and access to information. We recognized that now is the time to redo things.
We went live with Poka in Q1 of 2022. We started with around 150 users in our ceilings division and expanded that to a second plant, our gypsum division, for 295 users in total. But we see opportunities to push Poka into other areas of our business and more plants.
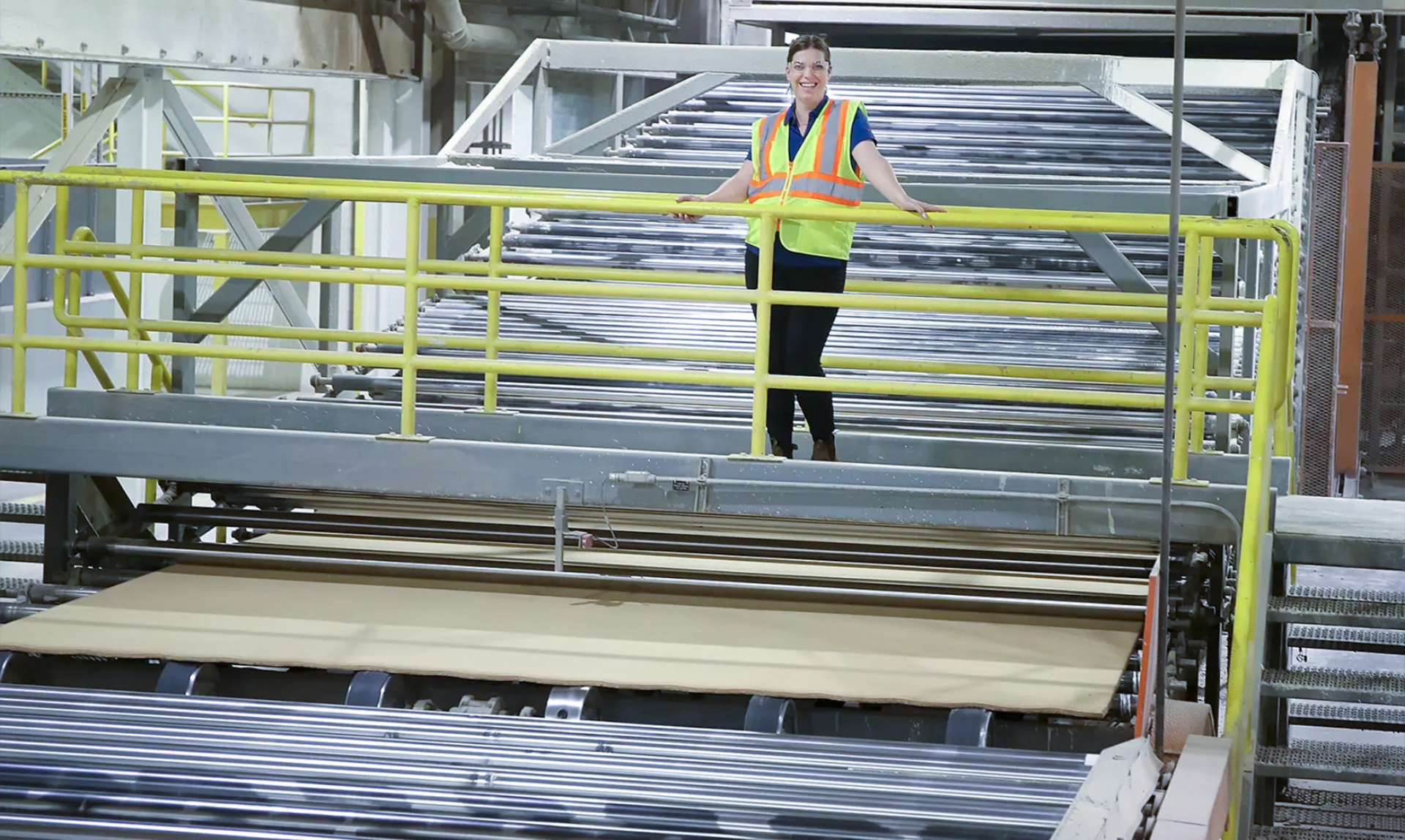