Benefits
Operational Support
Westrock employees’ knowledge continually improves, ensuring optimal and safe productivity. In addition, Poka’s collaboration tool has dramatically impacted the working environment and employee communication.
Standardization Of Training Content
Thanks to Poka, considerable time is saved in training employees. Staff can access equipment operations content, reducing downtime caused by human error. In addition, retirement is less of a concern, as the operational expertise held by the most experienced employees is now well-documented in Poka.
Health And Safety
An operator’s “dead time” is now used to carry out preventive maintenance procedures on their equipment, ensuring safer operations.
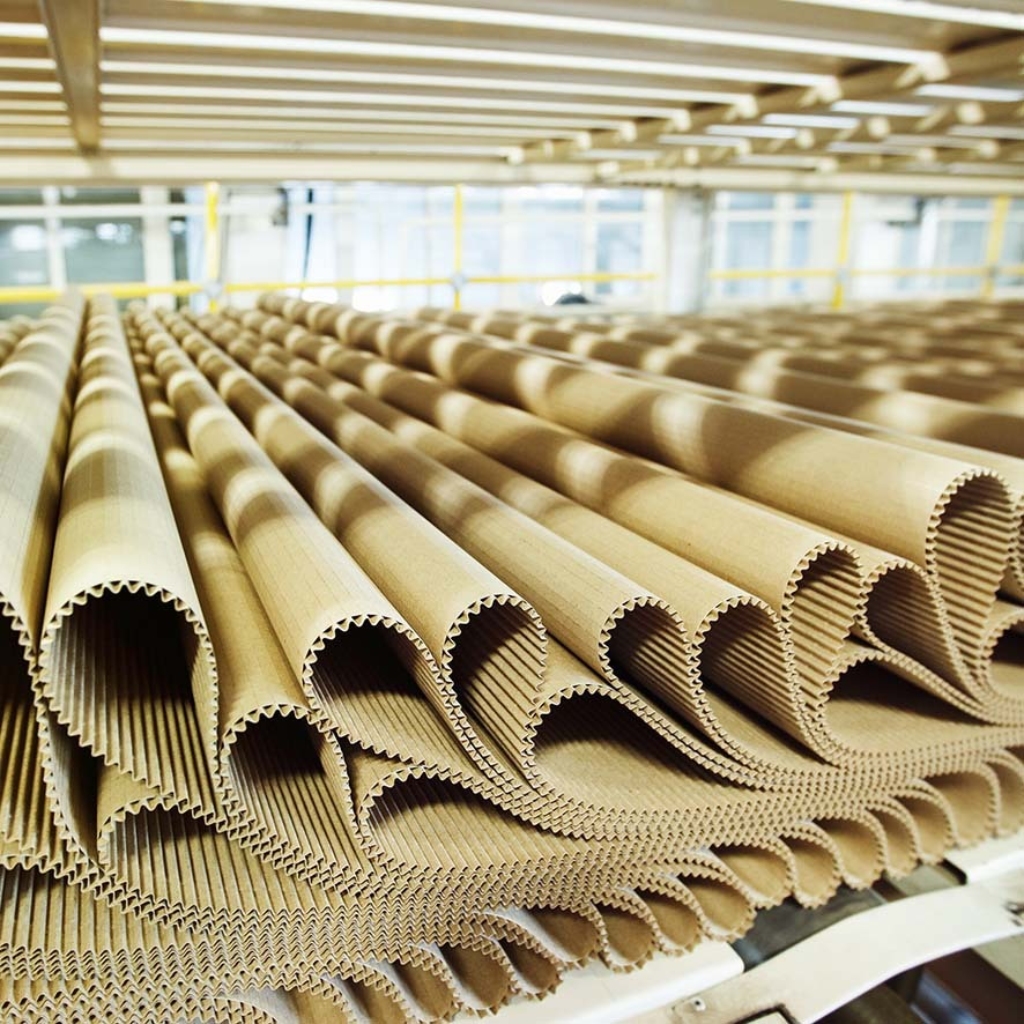