Resources
What's Included in the 5S Audit Checklist Package?
Get everything you need to implement a lean manufacturing culture at your plant. Our package includes:
- A complete 5S audit checklist (PDF, Excel)
- Beautifully designed posters to display in your plant
(Available in 24 x 36 in. and 8.5 x 11 in. sizes, ready for printing) A detailed handbook to help you get started
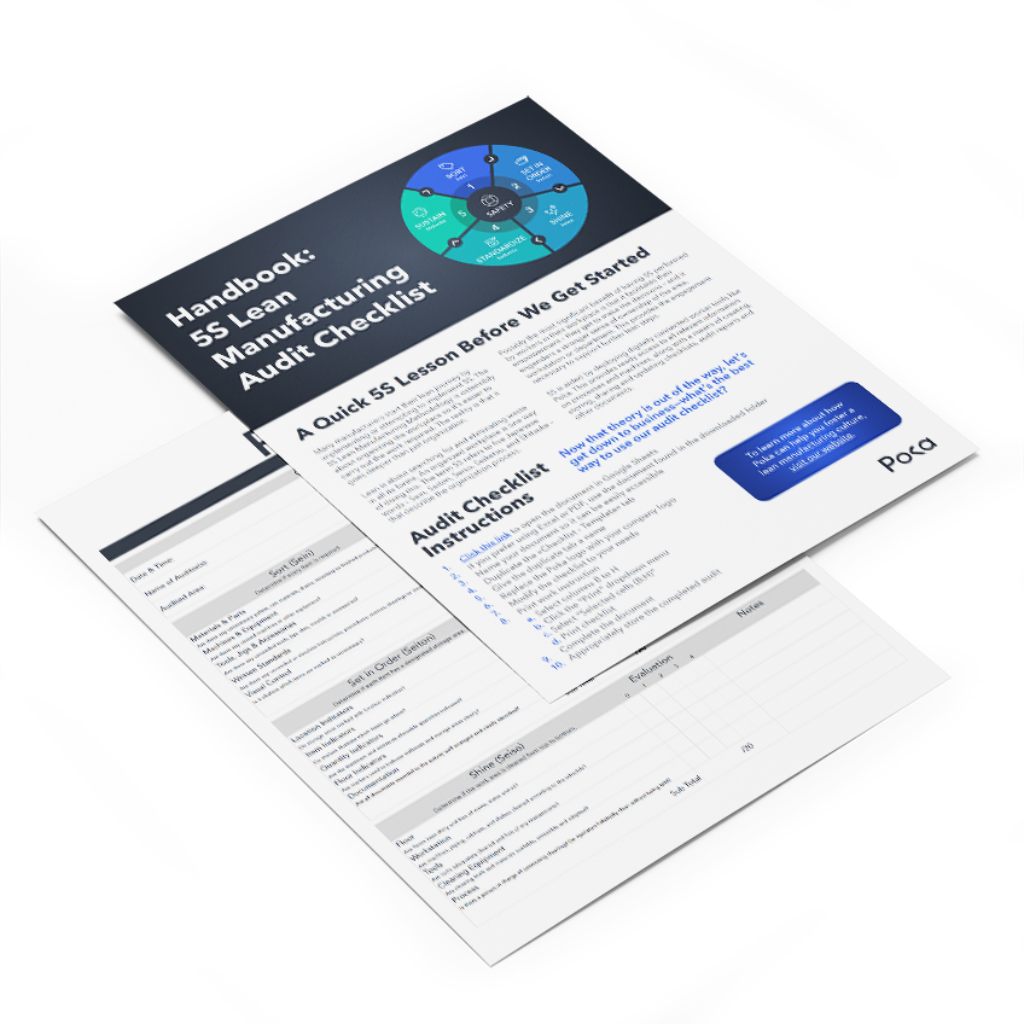