HOW WE HELP
Skills
Upskill and train operators to the standard and incorporate best practices
Exams, assessments and endorsements adds accountability and supports consistency
- Easily identify and assess the knowledge gaps with the skills matrix
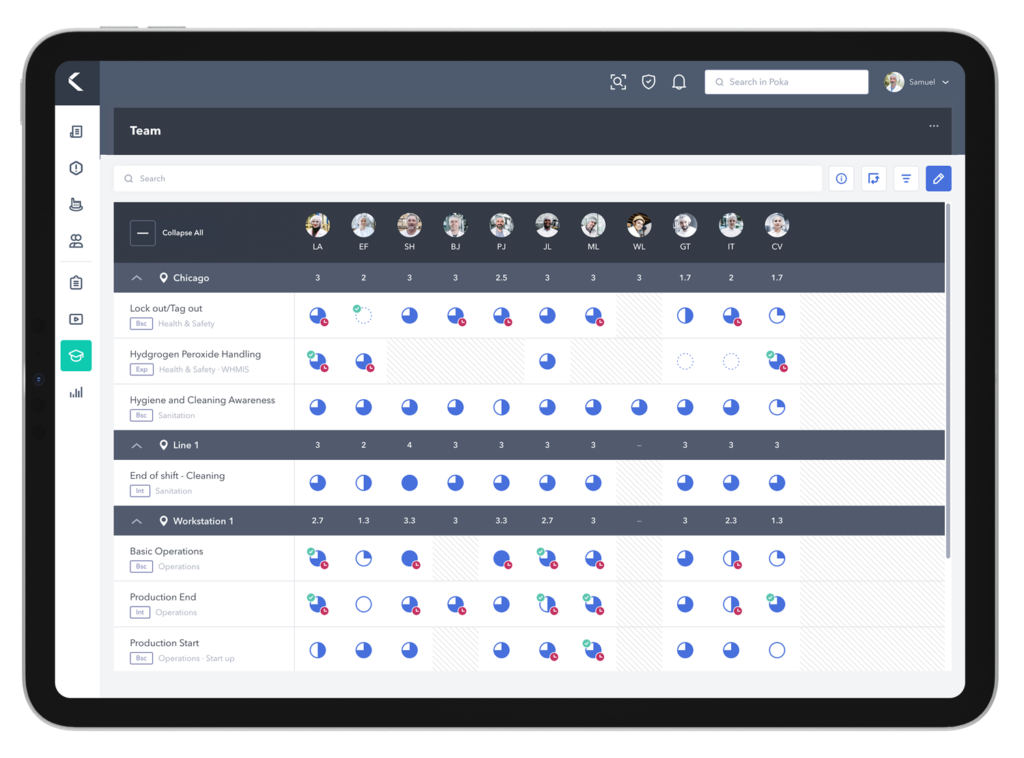